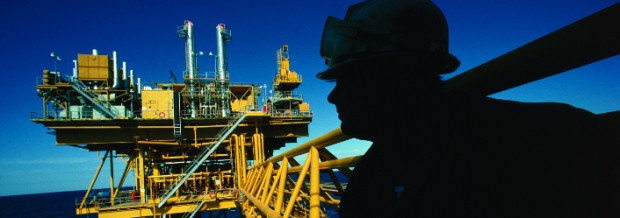
Industry figures reveal alarming maintenance trends
Recently published figures for oil and gas safety and industry performance show that the number of man hours for corrective and deferred maintenance, per North Sea installation, has increased year-upon-year. Â An increase in safety critical maintenance backlogs are of serious concern to the UKCS at time when the oil and gas industry is most vulnerable, but what can be done to reverse this trend?
Leading industry representatives Oil & Gas UK published figures which illustrate a rapid increase in uncompleted safety critical maintenance across North Sea installations. Findings revealed that deferred safety critical maintenance has steadily increased from nearly 1,000 man-hours to over 4,000 between 2009 and 2014. Whatâs more alarming is that an increase in the number of planned maintenance man-hours over the same period, has not reduced the number of corrective maintenance man-hours or cleared the safety critical backlog.
This data shows an increasing trend in planned, corrective and deferred safety-critical maintenance man-hours with predicted figures for 2015. Click on the image to view full leaflet of stats.Â
How did the industry arrive at this position?
Strategies for asset life extension are susceptible to widespread cost constraints, dictated by the current oil price volatility, but the backlog didnât appear overnight. Why did the number of man-hours continue to increase when the oil price averaged over $100 boe between 2011-13? Â Here are just some reasons Absoft has encountered as a leading SAPÂŽ consultancy in upstream oil and gas:
- Long lead times and a slow turnaround for the availability of safety critical equipment and spares to perform maintenance
- Maintenance plans which are not optimised can churn out spurious or duplicate work orders
- Lack of awareness and understanding of the Deferral Process
- Lack of sufficient training on data entry into maintenance management systems to record vital information
- Poor data entry into maintenance management systems due to complex ERP user interfaces and restricted time to perform the job
- Failure to flag work as complete – technicians donât register findings or maintenance team leads do not technically complete work orders
What will happen if this trend continues?
Itâs unthinkable. What the recent statistics tell us is that there is an endemic cycle of equipment failure in the UKCS. If the current trend continues, maintenance strategies will become more reactive to equipment malfunctions, with further delays to routine maintenance adding to the growing backlog.
Itâs inevitable that the risk of âfix on failureâ will have catastrophic consequences to safety, the environment and profitability. In response to these alarming figures, Absoft has made recommendations on how to improve the data quality associated with the backlog, and how to prioritise work orders to actively reduce deferred maintenance. At the same time, oil and gas companies need to prevent the backlog from building up again, and our blog offers solutions for improved data entry and streamlined maintenance processes.
How can we clear the safety critical maintenance backlog?
Absoft has developed an Asset Data Health Check which can evaluate whether maintenance master data is complete, accurate and compliant with industry standards. This periodic review has enabled Absoft to work with North Sea operators on: âClean the Messâ initiatives to identify redundant and obsolete work orders and prioritise deferred work orders based on safety, production and environmental levels of criticality.
Maintenance is deferred for a specific period of time based on a detailed risk assessment, but technicians need to consider resource availability, including other maintenance plans which occur around the same time of the deferral. Some companies use baselines like the volume in man-hours, to indicate when maintenance backlogs have reached critical mass, at which point, they will hire external contractors to execute large amounts of maintenance within a short timeframe.
In each case, the decision to defer maintenance should not be made in isolation. Partnering with Safran Solutions, Absoft offer integrated planning solutions which can manage critical interdependencies (like offshore bed space, economised shift patterns and resource conflicts between assets) to optimise maintenance planning and scheduling. SafranÂŽ Project⢠forms a seamless offering within Absoftâs SAP portfolio for upstream oil and gas, integrating with the SAP Plant Maintenance (PM) and Project Systems (PS) modules. The software provides powerful âwhat-ifâ scenario analysis which equip planners with flexible forecasting options to evaluate the cost and resource implications of deferring routine maintenance, compared with immediate action.
How can we prevent the backlog building up again?
Accurate data entry into maintenance management systems, or ERP, is the cornerstone of effective maintenance planning and scheduling. Without effective processes in place to pinpoint maintenance priorities and maximise resource allocation to complete these work orders, the frequency of equipment failure will increase, along with the cost of repair.
Absoft has developed a suite of custom web apps which can streamline maintenance processes and improve data entry using a simplified user interface, which is more aligned to the way oil and gas technicians operate. These web apps can be deployed on intrinsically safe ATEX Zone 1 mobile handhelds, or accessed from office desktops, at a relatively low cost of total ownership. The solution is proven to streamline corrective maintenance notifications across a paperless environment, in less administrative time and with increased accuracy. The simplified user-interface has also mitigated recurring technician training costs and the guided workflows have become widely adopted by maintenance teams to sustain effective data quality for the life of an asset.
What does the future hold?
Granted, planned and corrective maintenance figures are expected to rise for the majority of mature assets in the North Sea which continue to produce beyond their operational life. Yet, operators must react to the increasing safety critical maintenance backlog before the inevitable and unthinkable happens, forcing a step change across the industry.
Why Absoft?
My blog provides Absoftâs response on how to reduce safety critical maintenance backlogs, as a leading SAP consultancy with over 20 yearsâ experience in upstream oil and gas. Many of my SAP Plant Maintenance colleagues offer first-hand experience of upstream processes and our safety critical maintenance solutions comply with strict industry standards such as DNV-GL, ISO 14224 (Annex E) and NORSOK Z008. This combination uniquely positions Absoft to assist oil and gas companies to prevent the build-up of deferred maintenance and reduce backlogs before they reach tipping point.
Are you working to reduce a safety critical maintenance backlog? Is your asset data in need of a health check? Whatâs your opinion on the latest safety statistics released by Oil and Gas UK?
For more information about the topics covered in our blog, contact Absoft today via the button below or call +44 1224 707088 to speak with our SAP consultants.